
News
Underwater Weld Repairs – Requirements and Execution
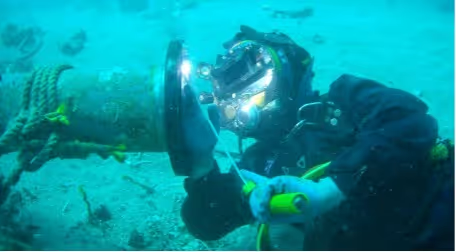
Introduction
Underwater welding, especially underwater wet welding, is gaining more and more acceptance. This is due not least to specially developed welding consumables, improved techniques and better training of the welder divers.
Corrosion and the associated need for maintenance as well as accidents on underwater structures that cannot be brought easily to the surface, such as: ships, structures in the offshore oil and gas industry and other areas of application require underwater welding work.
This article is a brief introduction to the differences between underwater dry and underwater wet welding, including their process limitations, with emphasis on underwater wet welding. The reader receives an overview of existing regulations, with the focus on the AWS D3.6M: Underwater Welding Code. The quality of underwater wet welded connections is illustrated using examples of afloat re pairs carried out on ships and on an off shore oil and gas floating asset.
Brief history of diving and underwater welding
Diving for the purpose of combat dates to the times of the Roman Empire and Ancient Greece. Plant stalks were used as snorkels. Over the following centuries, diving techniques and diving equipment were developed. While working in Venice, the “water city”, in 1500, Leonardo da Vinci designed his scuba gear for sneak attacks on enemy ships from underwater. In 1829, the first diving helmet was designed and built by Charles Anthony and John Deane from Whitstable in Kent, England. In 1843, the Royal Navy founded the first diving school.
At the beginning of the 20th century, professional diving had already been around for hundreds of years, but under water welding had not yet been developed. This changed when Konstantin Konstantinovich Khrenov, a Russian metallurgist, welding pioneer and university professor, developed a method for joining and cutting metals underwater and demonstrated it in 1932 with successful tests in the Black Sea. The first practical application of underwater wet welding took place in 1936 during the salvage of the merchant ship “SS Boris” from the Black Sea.
During World War II, underwater wet welding was used as an emergency re pair method and in salvage operations.
Cyril Jensen, a civil engineer and fascinated by Khrenov’s work, started an underwater welding program in the mid 1940’s as part of the US NAVY Experimental Station for Welding Research, in Annapolis, Maryland, USA.
In the late 1960’s and early 1970’s, under water wet welding gained further momentum with the emergence of the off shore oil and gas industry.
With the development of purpose build underwater wet welding electrodes, the development of underwater wet welder training curriculums and research aimed towards underwater wet welding, today we can produce wet welds comparable to their top site welded counterparts.
Types of underwater welding
Underwater welding can be broadly categorized into two main techniques: underwater dry welding and underwater wet welding. Each method has its own set of advantages, limitations, and applications.
Atmospheric underwater welding
Atmospheric underwater welding (one atmosphere welding) reproduces the atmospheric conditions of top site welding at the “underwater” work site. The work site is surrounded by a habitat designed to withstand the water pressure at the depth of the repair location. Once the habitat is installed and secured to the structure, it is drained and the internal pressure reduced to one atmosphere. The repair team can enter the habitat in a one atmosphere environment. Welding procedures and welding consumables developed for top site welding can be used, despite of those great advantages, one atmosphere systems have been little used.
Sealing the habitat to the structure can be challenging
Atmospheric welding underwater can also be carried out from within or with the help of a cofferdam. This is particularly suitable in tidal zones or at shallow water depths. The work site is surround ed by a cofferdam that is open to the surface or connected to the surface through a pipe with an access ladder. With the cofferdam to be open to the surface, the differential pressure is very low, almost balanced. Effective sealing techniques exist. This technology is very practical for specialized applications.
Hyperbaric dry welding
The technical compromise between wet and one atmosphere welding underwater is hyperbaric dry welding. The challenges associated with these two techniques are to eliminate the wet environment and the high pressure differential in the chamber. The repair site is surrounded within a working habitat, made of relatively lightweight materials, as it needs only to resist modest pressure differentials. The dewatering of the habitat is achieved by filling it with gas (breathing gas), which displaces the water.
The ambient pressure at which the weld ing is performed corresponds to the pressure at the work site. However, the increased pressures influence the reaction of gases, slag and metals in all weld ing processes. High density gases in crease the heat loss of the weld.
Hyperbaric dry welding using mini-/microhabitat
Using a mini or micro habitat, the diver is in the water while welding takes place in a dry environment. In the mini habitat, the electrode is inserted into the habitat through rubber grommets.
In the ©Micro Habitat, the electrode holder, the welding electrodes, the materials and the tools are stored inside the habitat.
The diver manipulates the electrode holder, electrodes and tools from the water side using permanently installed gloves, while watching through a window.
Hyperbaric wet welding
Hyperbaric wet welding is carried out at ambient pressure, with the welder diver in the water. There is no physical barrier between the water and the welding arc.
Hyperbaric wet welding – Factors influencing the weld quality
There are several different factors influencing the quality and the ease of production of underwater wet welding. The figure above gives an overview of the most important factors in question. In the following subsections of the influencing factors are briefly discussed.
Materials
Steels
Wet welding is performed in a wet environment that is “hostile” to both the weld and the welding process. Welding in a wet environment results in higher cool ing rates and produces significant amounts of martensite in the heat affect ed zone (HAZ) in almost all low alloy steels.
The IIW (International Institute of Welding) formula for calculating the carbon equivalent (CE) is used to determine the wet weldability of steels. Materials with a higher CE may have a highly martensitic microstructure and become increasingly susceptible to cracking. When the CE value of low carbon steels approaches 0.4, the fusion line hardness may exceed the HV 400 hardness value on the Vickers scale. The generally accepted CE upper limit for wet welding with ferritic electrodes is ≤ 0.4. The ideal materials for wet welding should have a CE ≤ 0.38 % and a carbon content of C ≤ 0.16 %.
Joint Geometry
Fillet welds
The root gap for a fillet weld should be kept to a minimum (approx. 1 mm). If the gap exceeds 2.5 mm, the gap should be reduced by buildup welding, rather than trying to bridge the gap with a single weld bead.
Always weld multi passes to increase weld ductility and strength due to tempering effect of subsequent weld passes, with three passes being a recommended minimum.
Groove welds
Penetration is extremely difficult to control in welds with an open root gap. If a partial joint penetration (PJP) is unacceptable, a fusible backing bar is required. To ensure good access to the root, a larger root opening is essential. If the use of a fuseable backing bar is not possible, the weld joint needs to be prepared with no root gap, but with a root face ≥ 3 mm. After welding the first side, the root side of the joint needs to be back gouged and filled with weld metal. If the root side is not accessible, either a doubler plate can be welded over the area to be repaired or, in the case of a pipe, a scalloped sleeve may be considered.
Welding positions
Underwater wet welding can be per formed, as top site welding in all positions, flat, horizontal, vertical and over head, with welding performed vertically, the progression will be downward (downhill). Due to the emerging upward traveling bubbles, the diver would not be able to see the weld joint. Welding down hill underwater will produce, unlike on top site a deep penetration, as shown in photograph below. Due to the fast-freezing weld puddle, welding downhill underwater will also be performed at a relatively slow travel speed.
Codes and specifications
In the following, codes and specifications related to underwater welding are being presented. What code or specification to be used is usually dictated by the project specifications, or other applicable rules or regulations.
AWS D3.6M: Underwater welding code
First published in 1983, AWS D3.6 became the industry standard for all welding operations under hyperbaric conditions, particularly wet welding. Subsequent editions of the standard were published in 1989, 1993, 1999, 2010. The current edition was published in 2017. The next edition is planned to be published in 2025.
The current edition of AWS 3.6 specifies three quality classes (A, B and O). These three quality classes cover the spectrum of quality and properties that can currently be achieved by underwater welding in both dry and wet environments.
Each weld class defines a set of criteria for weldment properties that must be established during qualification, and a set of weld soundness requirements that are to be verified during construction. The standard does not address the selection of the class that meets the service requirements of a particular application. The selection of the class of weld to be provided is to be determined by the customer or regulatory body.
A weld class specifies a level of serviceability and a set of required properties, as defined by mechanical tests, surface appearance, and nondestructive examination requirements, to which welds of a given class must conform.
There are three weld classes to choose from.
- Class A
Welds suitable for applications and design stresses comparable to conventional surface welded counterparts by virtue of specifying comparable properties and testing requirements. - Class B
Intended for less critical applications where lower ductility, moderate porosity and other limited discontinuities can be tolerated. - Class O
Class O underwater welds must meet requirements of another designated code/ standard, as well as additional requirements, specified in AWS D3.6, to deal with the underwater welding environment.
ISO standards for underwater wet welding
- ISO 15618-1:2016 Qualification testing of welders for underwater welding – Part 1: Hyperbaric wet welding;
- ISO/DIS 156149 Specification and qualification of welding procedures for metallic materials — Welding procedure test — Part 9: Underwater hyperbaric wet welding. (scheduled to be published at the end of 2024 or during 2025).
EWF European Federation for Welding, Joining and Cutting
- EWF570r114/SV00 Minimum requirements for the education, examination and qualification of European Manual Metal Arc (MMA)Diver Welder.
DIN standards for underwater wet welding
- DIN 2302:2005 Schweißzusätze Schweißzusätze für das Nassschweißen unter Überdruck von unlegierten Stählen und Feinkornstählen Abnah mebedingungen für die Prüfung und Qualifizierung von Schweißzusätzen für das Nassschweißen unter Überdruck (zurückgezogen) (Welding consumables – welding consumables for underwater hyperbaric wet welding of non-alloy and fine grain steels – Acceptance specifications for testing and qualification) (with drawn);
- DIN 2302:2018 Schweißzusätze - Umhüllte Stabelektroden zum Licht bogenhandschweißen von unlegierten Stählen und Feinkornstählen in nasser Überdruckumgebung — Einteilung (Welding consumables — Covered electrodes for manual metal arc welding of non-alloy and fine grain steels in a wet hyperbaric environment — Classification);
- DIN EN ISO 15618-1 Prüfung von Schweißern für Unterwasserschweißen — Teil 1: Unterwasserschweißer für Nassschweißen unter Überdruck (Qualification testing of welders for underwater welding — Part 1: Hyperbaric wet welding).
AWS standards
- AWS D3.6M:2017 Underwater Welding Code;
- AWS A5.35/A5.35M: 2015 Specification for Covered Electrodes for Underwater Wet Shielded Metal Arc Welding.
DVS guidelines and standards
- Richtlinie DVS 1801 Anforderungen an Betriebe und Personal für das nasse Unterwasserschweißen – Hersteller qualifikation (Requirements for com panies and personnel for underwater wet welding – manufacturer qualification).
- Richtlinie DVS 1811 Lichtbogen schweißen unter Wasser (Underwater arc welding);
- Merkblatt DVS 1812 Arbeitsschutz beim Unterwasserschweißen und schneiden Safety in underwater wet welding and cutting).
- Merkblatt DVS 1813 Unterwasser Lichtbogenhandschweißen mit um hüllten Stabelektroden (Manual under water arc welding with covered stick electrodes).
- Merkblatt DVS 1814 Gefahren durch elektrischen Strom beim nassen Unterwasserlichtbogenschweißen und not wendige Schutzmaßnahmen (Electrical shock hazards while manual underwater wet welding and required protective measures).
Environment
Environmental influences can significantly affect both the welding process and the quality of the weld produced. Some of these challenges are:
- Water depth: Water depth has a direct impact on weld quality and is an essential variable in the Welding Procedure Specification (WPS). As depth in creases, micropores increase and ductility decrease;
- Visibility: Visibility has a direct impact on weld quality. Restricted visibility can affect the welder diver’s ability to see the arc and inspect the resulting weld;
- Water or ship movement: Has a direct impact on the quality of welding. Swells, waves, water currents or the movement of the ship can have a detrimental effect on the welder diver to remain stable;
- Contamination: A special diving suit that restricts freedom of movement may be required.
- Access: Is the joint to be welded accessible to weld according to the WPS?
Personell/Training
Wet welder training provides opportunities to learn and experiment with the wet welding process while being under tuition. Historically and currently, it is commonly assumed that qualified and experienced top site welders can easily apply his/her skills underwater without the need for further training. Experienced top site welders may find it difficult to break habits that work fine on the surface but may be difficult if not impossible to apply underwater.
Underwater wet welding electrodes
Historically wet welding was completed using surface welding electrodes that were modified to keep the flux in place underwater during welding by applying electrical tape, wax, lacquer or paint to the flux. Some of these electrodes produced reasonably looking welds but their mechanical properties and user friendliness were comparatively poor. The development of new purpose-built welding electrodes improved the weld quality significantly.
Almost all underwater wet welding is performed with the shielded metal arc welding (SMAW111) process. Extensive research was performed regarding underwater wet welding with the flux cored arc welding (FCAW) process. The development of welding equipment for FCAW is still ongoing.
Welding equipment
For underwater wet welding, the type and condition of the welding equipment is essential. Poorly maintained or damaged equipment can affect arc performance and the quality of the resultant weld, in particular the equipment which is submerged underwater such as: Welding cables, connectors, electrode holder, earthing clamp/plate. Current leakage through the water will reduce the amount of current getting to the tip of the electrode and may/likely result in electric shock to the diver.
Case studies
The following 3 case studies describe briefly three types of underwater wet weld repairs performed on different as sets over time periods ranging from 6 port stops to 5 years.
Underwater wet weld repair– build-up welding
An inspection dive performed on the two rudders of a 290 m long cruise ship with a gross tonnage of 113,323 t revealed heavy cavitation and erosion damage on both the port and the starboard side rudders. When the damage, caused by galvanic corrosion was discovered, the ship was out of dry dock for appr. 3 months. Corrosion was observed in several areas on both rudders, ranging from mild corrosion to 100 % section loss. The repair was performed by cropping wasted sections and by buildup welding using underwater wet welding techniques. In addition, the starboard side rudder was filled with water and had to be de-watered after the repair.
SGS together with the cruise line and the classification society developed a repair plan involving the qualification of under water wet welded groove weld procedures to the class A requirements of AWS D3.6. In addition to the groove weld procedures welded in the flat, horizontal and vertical position, we also had to qualify “buildup welding”. Together with class, we decided on a plate with a machined “gap” to be filled with weld metal, to simulate building up wasted material to the original material thickness. Those test plates had to be welded in the vertical and the horizontal position. The welding of one “buildup” welding test plates took approx. 16 hours.
Over a period of three months an SGS crew sailed with the vessel. During regular port stops divers were deployed to restore the wasted material to its original plate thickness. The final repair was considered permanent and was performed without interrupting the itinerary of the vessel.
Underwater wet weld repair - skegg replacement
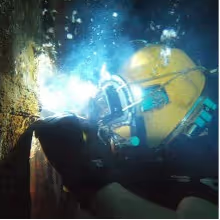
During a night grounding the skeg of a 325 m long cruise ship with a gross tonnage of 145,655t, was ripped off from the starboard azimuth thruster, a marine propulsion unit consisting of a fixed pitch propeller mounted on a steerable gondola (“pod”) containing the electric motor driving the propeller, allowing ships to be more maneuverable.
SGS worked together with the Original Equipment Manufacturer (OEM) and the Cruise Line to install a new skeg.
A new skeg was manufactured by the OEM and welded with a complete joint penetration (CJP) weld by SGS welder divers to the bulkhead on the bottom of the housing of the thruster, employing underwater wet welding techniques.
SGS welder divers sailed with the vessel and the repairs were performed during regular port stops, without interrupting the itinerary of the vessel.
Underwater wet weld repair - bilge keel repair
During the conversation from a tanker to a floating production storage and offload ing (FPSO) unit, the bilge keel of the former very large crude carrier (VLCC) with a length 274 meter and a gross tonnage of 132,361 t was modified. The modification consisted of an increase in bilge keel width from 600 mm to 1,200 mm and an increase in length from 102 m to 165 m. A bilge keel is a nautical device to reduce the rolling motion of a ship.
Design flaws together with poor workmanship caused the bilge keel to fracture during operation in several locations.
SGS worked together with the owner and the classification society to perform permanent underwater wet weld repairs on the fractures, without interrupting production.
A total of 30 High Priority Repairs (number 1 priorities) on the PORT and STBD side were identified and required under water wet weld repairs. In addition to the number 1 priorities, two number 2 priorities and 120 number 3 priorities, consist ing of 120 welds, to seal faying surfaces were identified. Number 3 priority welds were not structural and served only sealing purposes. A “priority” was identified as a “location” on the bilge keel that would require repair on one or multiple fractures. The type of priority (1, 2 or 3) was determined by the builder of the FPSO, the owner, class and SGS.
The priorities for the sequence of the repairs were based on discussions among the builder, the owner and SGS. The most influential factor in determining the sequence of the repairs was the criticality of the damage. A critical damage was defined as:
- Crack growth rate.
- What were the consequences if failure of the part occurred?
- Location of the damage on the bilge keel.
The underwater wet weld repair of the bilge keel of the FPSO started at the end of 2015 and was completed in April 2021. This was the first time that a repair of this magnitude was successfully completed by employing underwater wet welding techniques with the approval of a classification society.
After completion, all welds were subject to visual and magnetic particle inspection. In addition to the final inspection after completion of each repair, the 5 oldest repairs were selected (three on the PORT side and two on the STBD side) for additional visual and magnetic particle inspection. When the additional NDE was performed, the selected repairs were in service between 1075 and 1492 days, exposed to high hydrodynamic forces. No rejectable indications were observed.
All reported fractures were repaired and subject to visual and magnetic particle inspection and received final approval from the American Bureau of Shipping (ABS) and the Brazilian NAVY.
Summary
With the introduction of specially de signed underwater welding electrodes, improved techniques and better training, permanent repairs can be achieved using hyperbaric wet welding. As mentioned earlier in this paper, underwater wet welds comparable to their top site welded counterparts regarding mechanical properties and meeting NDE requirements can be produced.