
Case Study
Shell Plate Repair Afloat on an Offshore Supply Vessel
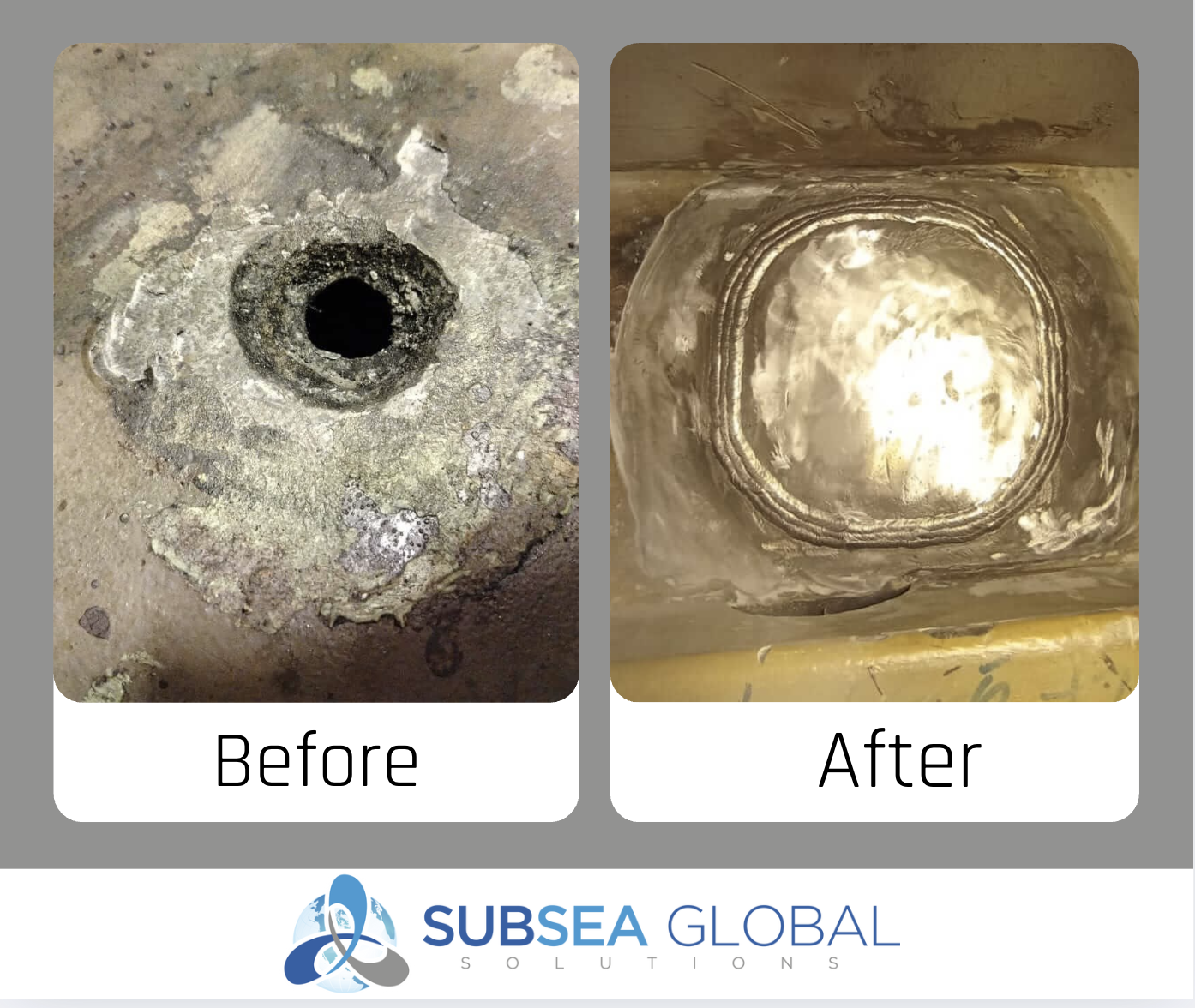
When a 90-meter offshore supply vessel discovered a corrosion hole in the bottom plating of its bilge tank, Subsea Global Solutions was called upon to deliver a class-approved repair solution. The 90 meter long and 19 meter wide vessel had developed a corrosion hole in the bottom plating of the bilge water tank underneath the sounding pipe. Our team in Trinidad mobilized to replace the worn shell plate section with an insert plate, ensuring the vessel was restored to operational readiness with minimal downtime.
Details of the Work
The repair process began with an assessment of the damage. Subsea Global Solutions worked closely with the owner of the vessel and the applicable classification society to confirm the extent of the damage. Based on the assessment, a repair procedure was written and submitted to the classification society for review and approval.
Preparation and Assessment
To begin the repair, Subsea Global Solutions obtained relevant drawings, ensuring the work would align with the original design and requirements of the classification society. An inspection was conducted together with a class surveyor to assess the extent of the damage and confirm the repair scope. Following the inspection, our team manufactured the required insert plate, large enough to replace the worn shell plate section and to meet the minimum class requirements for insert plates.
Repair Execution
To allow the replacement of the worn shell plate section, a cofferdam was installed by divers from the water side over the repair area. Once the cofferdam was in place and sealed against the hull it was dewatered, and the worn section of the bottom plating could be removed from the inside of the bilge water tank. The outer perimeters of the cut-out of the bottom plating as well as the outer perimeter of the insert plate were prepared with a weld joint preparation for a complete joint penetration (CJP) weld. The insert plate was fitted and tack welded in position with a consistent root opening. Subsea Global class-certified top side welders installed the insert plate with a CJP weld, based on our class approved top side procedures.
Quality Assurance
To ensure compliance with class rules and regulations, non-destructive testing (NDT) was performed on the welds in the form of 100% visual testing (VT), magnetic particle testing (MT), and ultrasonic testing (UT). After passing NDT, the cofferdam was removed and protective coating was applied to the repaired area from the inside of the vessel and from the water side, completing the repair process.
Conclusion
The Subsea Global Solutions Trinidad team successfully completed the repair, ensuring compliance with class regulations. The repair demonstrated our ability to execute class-approved repairs while minimizing vessel downtime. The client expressed satisfaction with the timely and professional execution of the work, reinforcing Subsea Global Solutions as a trusted partner for underwater repairs.
Underwater Repair Services
Subsea Global Solutions specializes in hull repairs and other maritime repair services, offering precision and efficiency to restore vessel integrity and performance. Whether addressing structural damage, corrosion, or other critical issues, our skilled teams use advanced techniques and class-approved procedures to deliver durable, high-quality solutions. From initial inspections to welding and finishing, every step is executed with attention to detail to ensure compliance with industry standards and class rules and regulations. Trust Subsea Global Solutions for reliable repairs that minimize downtime and keep your vessel operating at its best.
Request a Service
Need expert underwater repairs? Contact Subsea Global Solutions today to learn how we can assist with your vessel’s needs. Reach out to our team to schedule a consultation.