
Case Study
Subsea Global Solutions Repairs Hull Fracture in way of Bilge Keel
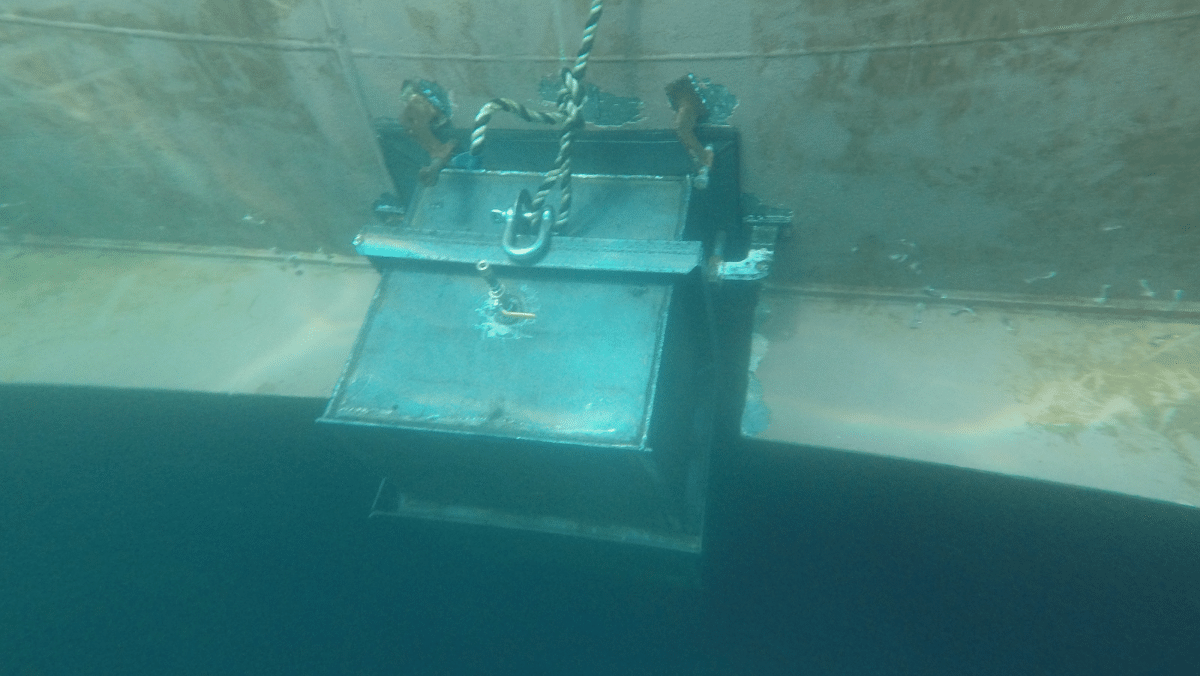
Problem
A client contacted Subsea Global Solutions to perform an underwater repair for its vessel’s pre-existing hull fracture while at the Rustin Anchorage in Tacoma, Washington. This fracture had been temporarily repaired during the vessel’s port call in China and was 550 mm in length located in the starboard side shell plate at the turn of the bilge, and propagated through the bilge keel and grounding bar. Our client required a solution that would serve as a class approved permanent repair and remove the Condition of Class (COC).
Solution
The Subsea Global Solutions centralized Technical Repair Department provided the client with a class approved permanent repair solution. The proposed permanent repair solution consisted of Subsea Global Solutions providing all of the services to remove the fracture permanently with the installation of a hull insert. As required by class, Subsea Global Solutions' in house welding engineer drafted a repair procedure which detailed the scope of work and included documents like class approved welding procedures and welder qualifications for underwater welding, dry welding, NDE procedures, material certificates, and more. The client then submitted the procedure to class for pre-approval which gives the client assurance that the COC will be removed upon successful completion of the permanent repair. Subsea Global Solutions mobilized a single team from the Subsea Global Solutions Port Angeles office composed of one project manager and four commercial diver technicians to complete the works in 6 x 12-hour shifts. The client preferred a single team for this specific project to manage the cost since the vessel had the time to remain in port for the duration of the repair.
We began the operation inside the vessel by templating the immediate area of the hull around the existing fracture. The hull templating serves two purposes, it tells the size and geometry of the insert plate and it provides us with the surface area and geometry needed to fabricate the cofferdam onsite. Once the hull templating was completed, the insert plate was rolled offsite and fabrication of the cofferdam began. To maximize efficiency, we divided the team to get divers in the water for removing the bilge keel and grounding bar in way of the hull fracture and planned cofferdam location. The removed grounding bar and bilge keel sections did not require replacement, so we continued as planned with diving operations and had the internal team working on the internal fractured frames. For the hull insert plate repair, we then positioned the cofferdam in place against the hull ensuring that the perimeter exceeded the hull insert size by 250 mm from the points of welding and secured it with welded screw dogs. With the cofferdam de-watered and securely in place, the internal team began removing the damaged hull plate and installing the insert plate. Meanwhile, the dive team began profiling the new established ends of the grounding bar and bilge keel sections against the hull. The welding of the grounding bar ends to the hull plating was performed using class approved underwater welding procedures in accordance with the Class A requirements of AWS D3.6M: Underwater Welding Code. Once the internal team finished the welding of the hull insert, they installed a new internal longitudinal frame between the internal web frames, running fore and aft to compensate for the bilge keel section removed. The internal welds where NDE tested to the satisfaction of the attending class surveyor employing UT shear wave inspection. After successful completion of the NDE and acceptance from the attending class surveyor, the dive team removed the cofferdam and successfully performed Magnetic Particle Inspection (MT) on the underwater welded fillet welds between the bilge keel grounding bar and the hull plating. Corrosion protection was applied over all areas of damaged coating.
Conclusion
The hull insert repair was completed with a single team of commercial divers/topside welders over 6 days despite the additional fracture repairs that were not included in the planned project scope. Subsea Global Solutions managed both, the underwater and internal portions of this repair to ensure each phase was executed seamlessly and to the satisfaction of attending class surveyor. Having a centralized Technical Repair Department does make a difference when managing complex underwater repairs on a global scale, as it allows Subsea Global Solutions to ensure both our clients and class receive the same familiar experience from Subsea Global Solutions they are accustomed to, regardless of where the project is taking place.