
Case Study
Subsea Global Solutions Restores Heavily Corroded Rudder
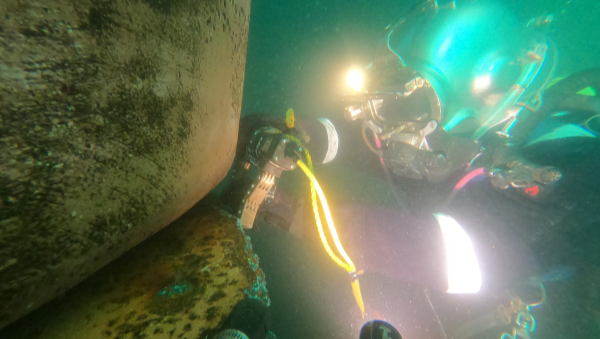
Problem
Subsea Global Solutions performed a rudder inspection with Class in attendance for a valued client’s vessel in Busan, Korea where we discovered the rudder was suffering from heavy erosion and cavitation damage. The areas effected included critical locations such as the port & starboard rudder plates, pintle lower casting in way of lower pintle, the edges on rudder bottom plate, the area in way of bottom plug, the end of upper and lower fin plates, and more. Considering there was not enough time to complete the underwater repairs before the vessel’s planned departure and a full underwater repair procedure needed to be written and approved by Class, a “Condition of Class” (COC) to our client’s vessel was issued by the attending class surveyor. The COC required a permanent repair of the wasted areas and the de-watering of the rudder blade within 30 days. Subsea Global Solutions requested the vessel itinerary and we identified the vessel would be visiting 2 out of our 13 wholly-owned offices within that 30-day time frame. Tampa, Florida, the vessel’s first call, had a limited port stop for such extensive repairs. The best option was Long Beach, California, where the vessel had a one-week time frame for cargo operations without needing to go off-hire.
Solution
The initial inspection report from Subsea Global Solutions Busan was delivered to our centralized Technical Repair Department to develop a cost-effective repair solution that would remove the COC and enable the vessel to continue sailing for the next 28 months until the next scheduled dry dock. Per usual protocol, the underwater repair procedure was submitted to Class for review and approval. The wet weld repair was mainly based on our Class approved “build-up” wet welding procedure (as referenced in the Subsea Global Solutions Case Study: Galvanic Corrosion on Both Rudders), which is a pioneered methodology established by Subsea Global Solutions together with class to restore wasted steel plating to its original cross section. The underwater repair procedure was approved with minor adjustments including the extraction of steel samples from the rudder material to determine it’s wet weldability as well as additional non-destructive examination (NDE).
The repair was based on underwater welding only, eliminating the need for the installation of open top cofferdams or other barriers that would allow dry welding repairs to take place, which requires more time and resources. Subsea Global Solutions Long Beach mobilized two 5-man teams of commercial divers and welder divers to operate around the clock during cargo operations until the underwater repair was concluded. We began the repair process by removing the 2 existing rudder fins that were heavily corroded. Next, we prepared each of the wasted areas of the rudder for build-up welding by cleaning them to bare metal using underwater grinding and brushing methods. This allows us to start with an even and clean surface to restore the wasted areas to the original plate thickness. Once each area was prepared, we began to build-up the affected areas with weld metal using our class approved welding procedures specification's (WPS). All our underwater Class approved wet welding procedures are based on the Class A requirements of AWS D3.6M: Underwater Welding Code. Once the wasted areas of the rudder were restored to its original cross section, by build-up welding, visual (VT) and magnetic particle inspection (MT) were performed. Once the repairs passed NDE, the rudder was dewatered, and corrosion protection was applied over at each repair location.
Conclusion
Having a centralized Technical Repair Department really does make a difference in managing complex underwater repairs on a global scale. This allows Subsea Global Solutions to ensure both our Clients and Class receive the same familiar experience from Subsea Global Solutions they are used to, regardless of where the project is taking place. The vessel had one week available in the Port of Long Beach—but we completed this underwater repair in three days. As always, we strive to be our clients’ most valued resource and in the end, the project was completed to the client's satisfaction within the planned timeline in a safe, professional, and efficient manner.
Our goal is to always deliver unrivaled service. From hull maintenance to complex ship repair, there is only one global resource you can truly rely on; Subsea Global Solutions.