Underwater Welding & Hull Repairs
Subsea Global Solutions has an unparalleled technical capabilities for all your underwater welding and hull repair needs.
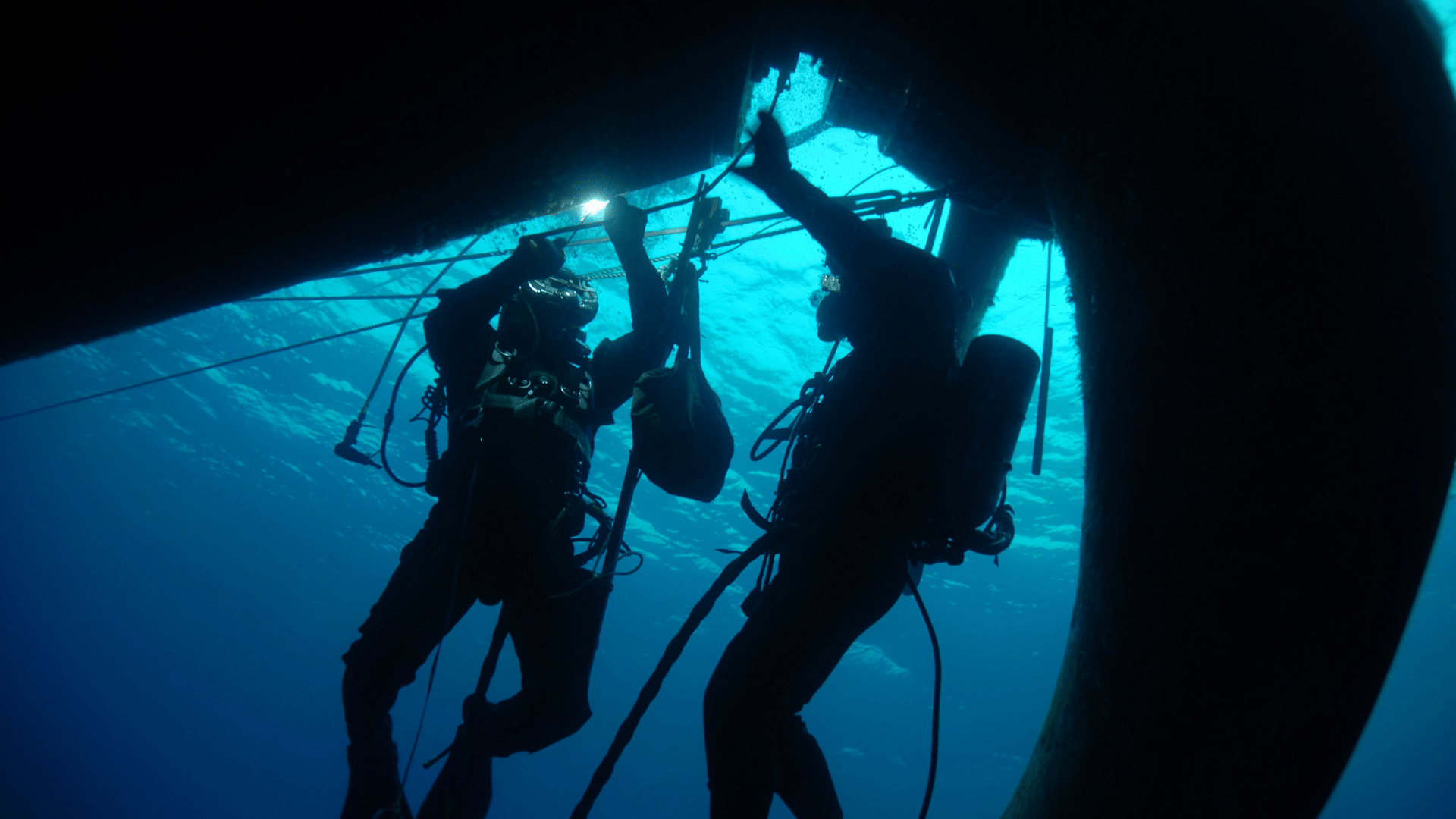
.truncate { white-space: nowrap; text-overflow: ellipsis; }
Class approved permanent repair processes are established using underwater wet welding, atmospheric dry welding or hyperbaric dry welding for permanent repairs to incidental hull damage below the water line. With an in-house Engineering department headed by our Senior Welding Engineer, who has decades of welding experience on topside and underwater, Subsea Global Solutions is capable of Structural Engineering and writing repair procedures detailing the welding process and scope of repair to be developed upfront for pre-approval by Head Offices of major Classification Societies or insurance underwriters. Having a pre-approved repair procedure by the Class damage department gives the customer a guarantee that a permanent repair is achieved on time wherever or whenever required.
Welder/Diver technicians are trained, qualified and their qualifications renewed every 2 years in one of the three training tanks at Subsea Global Solutions facilities. All welders WPQR’s are done on Classification Society certified paper to the Class A requirements of AWS D3.6M: Underwater Welding Code.
Subsea Global Solutions is the only diving company globally to have a Workshop Approval for Underwater Welding by DNV.
Subsea Global Solutions designs and manufactures cofferdams of all sizes and configurations. Well versed in the development of flexible as well as rigid hyperbaric (open bottom) or atmospheric cofferdams.
Learn more about Underwater Blankings & Cofferdams
Learn more about Underwater Welding in this Build-up Underwater Welding Repair
Hydroweld FS wet underwater welding electrodes are the result of significant research and development into flux formulations, filler metals and supplementary coatings. They are designed to work in all positions in fresh water, brine or saltwater, and have been used to successfully perform wet weld repairs have been performed to a depth of 300 meters. Their outstanding user-friendly properties and wet welding characteristics, easily produce high quality wet welds to internationally recognized standards. Hydroweld FS is the electrode of choice where high-quality wet welding is required. They have meet the class A requirements of AWS D3.6M for fillet and groove wet welds as has been witnessed by Lloyds Register of Shipping (LR), American Bureau of Shipping (ABS), Det Norske Veritas (DNV), Bureau Veritas (BV), and Rina. Hydroweld FS wet welding electrodes are currently the only wet underwater welding electrodes approved for permanent and temporary repairs on war ships by the British Ministry of Defense (MoD). This was gained after intensive underwater comparability testing and further NDE and destructive testing against all other commercially available wet welding electrodes by the MoD and The Welding Institute (TWI). As a result, the electrodes are now included in the NATO codification system.
Enjoy our short trailer on Offshore Asset Maintenance services.
Enjoy our short trailer on our Cleaning Remote Operated Vehicle, the PORTABLE C-ROV, ideally suited for heavier macrofouling before repositioning your vessel or offshore asset.
We're proud to spotlight Uwe Aschemeier, our Head of Welding Services. With extensive experience as a commercial diver, Uwe is also an award-winning educator and a respected speaker in the underwater welding industry, known for his dedication to advancing industry standards and sharing his expertise worldwide.
View Full Case StudyIn October, Subsea Global Solutions held its advanced underwater welding training course in our training center in Long Beach, providing a comprehensive 10-day program designed to hone practical skills and qualify participants for new joint geometries and/or new welding positions.
View Full Case StudyUnderwater welding, especially underwater wet welding, is gaining more and more acceptance. This article from Welding & Cutting Magazine takes a deep dive into types, procedures, and codes.
View Full Case Study3 month out of dry dock, galvanic corrosion caused heavy cavitation/erosion damage on PORT and STBD side rudders.
View Full Case StudyDuring cargo operations, a submerged pile pierced through the hull. Subsea Global Solutions worked together with owner and class to develop repair plan that included the design and installation of an engineered cofferdam.
View Full Case StudyA Blue-Chip oil & gas company incurred several defects and cracks in a critical attachment member of an FPSO’s hull – these defects required repair to allow continued operation.
View Full Case StudyDesign flaws together with poor workmanship caused the bilge keel to fracture during operation in several locations. Subsea Global Solutions worked together with the owner and Class to perform permanent underwater wet weld repair on the fractures, without interrupting the production.
View Full Case StudySubsea Global Solutions Halifax quickly resolved an oil leak crisis on a remote Canadian ferry with careful night repairs, revealing a deteriorated weld issue.
View Full Case StudyEfficient removal of anchor chain debris by Subsea Global Solutions before the vessel's planned departure. Trust our expertise for timely and reliable debris removal services.
View Full Case StudyThe benefits of removing a damaged bow thruster afloat are many. The customer was able to prevent further damage to the bearings and gears caused by the presence of seawater in the gear housing and the procedures allows the units to be overhauled prior to the vessels next dry-dock—or, they can be re-installed afloat by Subsea Global Solutions, which would help to eliminate the need for additional tug cost.
View Full Case StudyThe project was executed with two Subsea Global Solutions teams working around the clock. While the vessel trimming process was in motion, the team onboard the vessel began to drain the oil from the thruster while the dive team began removing the bow thruster tunnel gratings to gain full access to the bow thruster.
View Full Case StudyThe installation of complete SOx scrubber systems is entirely possible without taking the vessel out of the water. Subsea Global Solutions' involvement is focused on precision cutting of the hull penetrations for the sea chest openings and overboard spool pipe installation below the waterline.
View Full Case StudyDiscover our innovative scrubber installation solution without dry docking. Minimize downtime and costs while ensuring compliance. Learn more today.
View Full Case StudyWhen a roll-on/roll-off ship (RO-RO) required an immediate thruster installation and rudder bushing repairs, Subsea Global Solutions stepped in to deliver a seamless in-water solution.
View Full Case StudySubsea Global Solutions (SGS) recently completed a challenging underwater repair for a commercial ship owner whose vessel had suffered severe grounding damage including a badly damaged propeller, partial loss of the rudder horn, rudder damage, and even...
View Full Case StudyDryDock Magazine recently interviewed Harun (Aaron) Duzgoren (CCO), and Kevin Peters (Director, Technical Sales & Environmental Services) about a significant 100+ tonne rudder repair operation carried out afloat on a fully laden mainline container vessel.
View Full Case StudySubsea Global Solutions solves serious problems: Assisting a large fully laden Post-Panamax container vessel with steering issues. Subsea Global Solutions works with port authorities, class, and manufacturers to provide class-approved in-water float out removal, repair, and refit of a 110 mt rudder. Find out how our underwater inspection and survey services deliver practical, cost-effective solutions to a complex offshore problem. Subsea Global Solutions works with port authorities, class, and manufacturers to provide class-approved in-water rudder float out removal, repair, and refit of a 110 mt rudder. Helping owners safely reduce their risk exposure and related costs that would include diversions, delays, and downtime.
View Full Case Study3 months out of dry dock, galvanic corrosion caused heavy cavitation/ erosion damage on PORT and STBD side rudders.
View Full Case StudyAnother happy client back to business: 3800 CPM of sand & silt dredged in a short time window, and under budget! Read the full case study here.
View Full Case StudyWhen a propeller sustains damage beyond the straightening capabilities of even the largest press equipment, hydrodynamic corrections offer an innovative and effective solution.
View Full Case StudyNot all propeller damage can be straightened. When blades are fractured, chipped, or excessively bent, cropping becomes necessary. However, cropping an odd-numbered blade propeller presents unique challenges that must be carefully managed.
View Full Case StudySubsea Global Solutions’ proprietary propeller straightening technology offers a far more efficient and cost-effective alternative to blade cropping.
View Full Case StudyDiscover how Subsea Global Solutions swiftly resolved propeller damage for a heavy-load carrier in Palm Beach, restoring performance and efficiency with precision repairs.
View Full Case StudySubsea Global Solutions (SGS) recently completed a challenging underwater repair for a commercial ship owner whose vessel had suffered severe grounding damage including a badly damaged propeller, partial loss of the rudder horn, rudder damage, and even...
View Full Case StudySubsea Global Solutions can restore your propeller blades as a permanent repair, to OEM design geometry by cold static loading with our underwater propeller blade press.
View Full Case StudySubsea Global Solutions started its underwater repair process by establishing load-rated rigging points above the propeller using 4F Class A wet welding procedures to allow safe new replacement propeller blade transfer of the propeller blades.
View Full Case StudySubsea Global Solutions' propeller repair services in Canada, Panama, Uruguay, Singapore, and El Salvador. Explore our expert Diver's methods and tools.
View Full Case StudySubsea Global Solutions was tasked with completing a routine propeller polishing and hull inspection for a commercial vessel docked at the Port of Palm Beach. This service, part of the vessel’s ongoing maintenance schedule, ensured optimal performance and efficiency.
View Full Case StudyA big thank you to Captain Kate for sharing a behind-the-scenes look at Subsea Global Solutions in action on a propeller polishing project.
View Full Case StudyDiscover how Subsea Global Solutions swiftly resolved propeller damage for a heavy-load carrier in Palm Beach, restoring performance and efficiency with precision repairs.
View Full Case StudyBy utilizing a multi-stage polishing process and diver / technicians trained in the proper analysis of the propeller condition, Subsea Global Solutions' process has proven to be an integral part of fuel efficiency programs. The benefits of maintaining a polished propeller have been known for years, but what has not been known is "how smooth is smooth"?
View Full Case StudySubsea Global Solutions performs high-capacity underwater repairs worldwide. Discover the innovative techniques and use of TransHab for underwater seal replacement.
View Full Case StudyAs part of the cruise industry’s focus on the environment, a vessel operating in the South Pacific developed a minor problem with both of its shaft seals. Read how Subsea Global stepped in to provide a solution.
View Full Case StudySubsea Global Solutions fixed a special shaft seal issue on a loaded bulk carrier, stopping oil loss and water entry. Stern seal repair in Romania, Nov '17.
View Full Case StudyIn 2024, Subsea Global Solutions completed a complex overhaul of eight thrusters on the La Muralla oil rig, led by our Curaçao-based team, ensuring the rig's peak performance through rapid, on-site servicing.
View Full Case StudyClass approved shell plate underwater damage repairs to offshore semi-submersible platform without drydocking.
View Full Case StudyDryDock Magazine recently interviewed Harun (Aaron) Duzgoren (CCO), and Kevin Peters (Director, Technical Sales & Environmental Services) about a significant 100+ tonne rudder repair operation carried out afloat on a fully laden mainline container vessel.
View Full Case StudyThe installation of complete SOx scrubber systems is entirely possible without taking the vessel out of the water. Subsea Global Solutions' involvement is focused on precision cutting of the hull penetrations for the sea chest openings and overboard spool pipe installation below the waterline.
View Full Case StudyDuring cargo operations, a submerged pile pierced through the hull. Subsea Global Solutions worked together with owner and class to develop repair plan that included the design and installation of an engineered cofferdam.
View Full Case StudyA Blue-Chip oil & gas company incurred several defects and cracks in a critical attachment member of an FPSO’s hull – these defects required repair to allow continued operation.
View Full Case StudyDesign flaws together with poor workmanship caused the bilge keel to fracture during operation in several locations. Subsea Global Solutions worked together with the owner and Class to perform permanent underwater wet weld repair on the fractures, without interrupting the production.
View Full Case StudySubsea Global Solutions performs high-capacity underwater repairs worldwide. Discover the innovative techniques and use of TransHab for underwater seal replacement.
View Full Case StudyAs part of the cruise industry’s focus on the environment, a vessel operating in the South Pacific developed a minor problem with both of its shaft seals. Read how Subsea Global stepped in to provide a solution.
View Full Case StudySubsea Global Solution's impressive biofouling cleaning operation on a massive FLNG vessel in Busan. Explore the difficulties and creative approaches.
View Full Case StudyDryDock Magazine recently interviewed Harun (Aaron) Duzgoren (CCO), and Kevin Peters (Director, Technical Sales & Environmental Services) about a significant 100+ tonne rudder repair operation carried out afloat on a fully laden mainline container vessel.
View Full Case StudyThe installation of complete SOx scrubber systems is entirely possible without taking the vessel out of the water. Subsea Global Solutions' involvement is focused on precision cutting of the hull penetrations for the sea chest openings and overboard spool pipe installation below the waterline.
View Full Case Study3 month out of dry dock, galvanic corrosion caused heavy cavitation/erosion damage on PORT and STBD side rudders.
View Full Case StudySubsea Global Solutions can restore your propeller blades as a permanent repair, to OEM design geometry by cold static loading with our underwater propeller blade press.
View Full Case StudyThe benefits of removing a damaged bow thruster afloat are many. The customer was able to prevent further damage to the bearings and gears caused by the presence of seawater in the gear housing and the procedures allows the units to be overhauled prior to the vessels next dry-dock—or, they can be re-installed afloat by Subsea Global Solutions, which would help to eliminate the need for additional tug cost.
View Full Case StudyThe project was executed with two Subsea Global Solutions teams working around the clock. While the vessel trimming process was in motion, the team onboard the vessel began to drain the oil from the thruster while the dive team began removing the bow thruster tunnel gratings to gain full access to the bow thruster.
View Full Case StudySubsea Global Solutions started its underwater repair process by establishing load-rated rigging points above the propeller using 4F Class A wet welding procedures to allow safe new replacement propeller blade transfer of the propeller blades.
View Full Case StudySubsea Global Solutions performs high-capacity underwater repairs worldwide. Discover the innovative techniques and use of TransHab for underwater seal replacement.
View Full Case StudyA deep-sea bulk carrier fully loaded with goods had become immobilized due to a failure of the aft shaft bearing. In the past, not much could be done to help a vessel in this situation. With no way to transit on its own power and loaded with a perishable cargo, an economical solution needed to be developed quickly. Read more.
View Full Case StudySubsea Global Solutions' propeller repair services in Canada, Panama, Uruguay, Singapore, and El Salvador. Explore our expert Diver's methods and tools.
View Full Case StudyAs part of the cruise industry’s focus on the environment, a vessel operating in the South Pacific developed a minor problem with both of its shaft seals. Read how Subsea Global stepped in to provide a solution.
View Full Case StudySubsea Global Solution's impressive biofouling cleaning operation on a massive FLNG vessel in Busan. Explore the difficulties and creative approaches.
View Full Case StudyDryDock Magazine recently interviewed Harun (Aaron) Duzgoren (CCO), and Kevin Peters (Director, Technical Sales & Environmental Services) about a significant 100+ tonne rudder repair operation carried out afloat on a fully laden mainline container vessel.
View Full Case StudySubsea Global Solutions solves serious problems: Assisting a large fully laden Post-Panamax container vessel with steering issues. Subsea Global Solutions works with port authorities, class, and manufacturers to provide class-approved in-water float out removal, repair, and refit of a 110 mt rudder. Find out how our underwater inspection and survey services deliver practical, cost-effective solutions to a complex offshore problem. Subsea Global Solutions works with port authorities, class, and manufacturers to provide class-approved in-water rudder float out removal, repair, and refit of a 110 mt rudder. Helping owners safely reduce their risk exposure and related costs that would include diversions, delays, and downtime.
View Full Case StudyThe installation of complete SOx scrubber systems is entirely possible without taking the vessel out of the water. Subsea Global Solutions' involvement is focused on precision cutting of the hull penetrations for the sea chest openings and overboard spool pipe installation below the waterline.
View Full Case Study3 months out of dry dock, galvanic corrosion caused heavy cavitation/ erosion damage on PORT and STBD side rudders.
View Full Case Study3 month out of dry dock, galvanic corrosion caused heavy cavitation/erosion damage on PORT and STBD side rudders.
View Full Case StudyDuring cargo operations, a submerged pile pierced through the hull. Subsea Global Solutions worked together with owner and class to develop repair plan that included the design and installation of an engineered cofferdam.
View Full Case StudySubsea Global Solutions can restore your propeller blades as a permanent repair, to OEM design geometry by cold static loading with our underwater propeller blade press.
View Full Case StudyDesign flaws together with poor workmanship caused the bilge keel to fracture during operation in several locations. Subsea Global Solutions worked together with the owner and Class to perform permanent underwater wet weld repair on the fractures, without interrupting the production.
View Full Case StudyThe client indicated that the tailshaft had shifted aft approximately 200 mm when the ship’s crew was doing maintenance on the shaft coupling. It resulted in the aft water seal losing contact with the liner, causing large amounts of water ingress into the stern tube.
View Full Case StudyThe benefits of removing a damaged bow thruster afloat are many. The customer was able to prevent further damage to the bearings and gears caused by the presence of seawater in the gear housing and the procedures allows the units to be overhauled prior to the vessels next dry-dock—or, they can be re-installed afloat by Subsea Global Solutions, which would help to eliminate the need for additional tug cost.
View Full Case StudyThe project was executed with two Subsea Global Solutions teams working around the clock. While the vessel trimming process was in motion, the team onboard the vessel began to drain the oil from the thruster while the dive team began removing the bow thruster tunnel gratings to gain full access to the bow thruster.
View Full Case StudyThe client was in need of a turn-key—class approved—permanent repair. This included a single contractor that would manage the internal technical repair team, commercial diver team, prefabrication of the new spool pieces with flanges, final application of the 5-year warranty POLYFLAKE protective coating to 3000 microns on the new spool pipes, and achieving final class approval for the full repair procedure.
View Full Case StudySubsea Global Solutions successfully repairs hull fracture in the way of the bilge keel. Trust our expertise for reliable and efficient hull repairs. Learn more today.
View Full Case StudySuccessful completion of afloat rudder stock seal replacement by Subsea Global Solutions. Trust our expertise for reliable and efficient seal replacements.
View Full Case StudySubsea Global Solutions restores the heavily corroded rudder to optimal condition. Trust our expertise for effective and reliable rudder restoration services. Learn more today.
View Full Case StudySubsea Global Solutions started its underwater repair process by establishing load-rated rigging points above the propeller using 4F Class A wet welding procedures to allow safe new replacement propeller blade transfer of the propeller blades.
View Full Case StudySubsea Global Solutions performs high-capacity underwater repairs worldwide. Discover the innovative techniques and use of TransHab for underwater seal replacement.
View Full Case StudyA deep-sea bulk carrier fully loaded with goods had become immobilized due to a failure of the aft shaft bearing. In the past, not much could be done to help a vessel in this situation. With no way to transit on its own power and loaded with a perishable cargo, an economical solution needed to be developed quickly. Read more.
View Full Case StudySubsea Global Solutions' propeller repair services in Canada, Panama, Uruguay, Singapore, and El Salvador. Explore our expert Diver's methods and tools.
View Full Case StudyAs part of the cruise industry’s focus on the environment, a vessel operating in the South Pacific developed a minor problem with both of its shaft seals. Read how Subsea Global stepped in to provide a solution.
View Full Case StudySubsea Global Solutions fixed a special shaft seal issue on a loaded bulk carrier, stopping oil loss and water entry. Stern seal repair in Romania, Nov '17.
View Full Case StudySubsea Global Solution's impressive biofouling cleaning operation on a massive FLNG vessel in Busan. Explore the difficulties and creative approaches.
View Full Case StudySubsea Global Solutions Halifax quickly resolved an oil leak crisis on a remote Canadian ferry with careful night repairs, revealing a deteriorated weld issue.
View Full Case StudyAnother happy client back to business: 3800 CPM of sand & silt dredged in a short time window, and under budget! Read the full case study here.
View Full Case StudyTo learn more about underwater welding at Subsea Global Solutions, review our latest underwater welding case study.
Class approved permanent repair processes are established using underwater wet welding, atmospheric dry welding or hyperbaric dry welding for permanent repairs to incidental hull damage below the water line. With an in-house Engineering department headed by our Senior Welding Engineer, who has decades of welding experience on topside and underwater, Subsea Global Solutions is capable of Structural Engineering and writing repair procedures detailing the welding process and scope of repair to be developed upfront for pre-approval by Head Offices of major Classification Societies or insurance underwriters. Having a pre-approved repair procedure by the Class damage department gives the customer a guarantee that a permanent repair is achieved on time wherever or whenever required.
Welder/Diver technicians are trained, qualified and their qualifications renewed every 2 years in one of the three training tanks at Subsea Global Solutions facilities. All welders WPQR’s are done on Classification Society certified paper to the Class A requirements of AWS D3.6M: Underwater Welding Code.
Subsea Global Solutions is the only diving company globally to have a Workshop Approval for Underwater Welding by DNV.
Subsea Global Solutions designs and manufactures cofferdams of all sizes and configurations. Well versed in the development of flexible as well as rigid hyperbaric (open bottom) or atmospheric cofferdams.
Learn more about Underwater Blankings & Cofferdams
Learn more about Underwater Welding in this Build-up Underwater Welding Repair
Hydroweld FS wet underwater welding electrodes are the result of significant research and development into flux formulations, filler metals and supplementary coatings. They are designed to work in all positions in fresh water, brine or saltwater, and have been used to successfully perform wet weld repairs have been performed to a depth of 300 meters. Their outstanding user-friendly properties and wet welding characteristics, easily produce high quality wet welds to internationally recognized standards. Hydroweld FS is the electrode of choice where high-quality wet welding is required. They have meet the class A requirements of AWS D3.6M for fillet and groove wet welds as has been witnessed by Lloyds Register of Shipping (LR), American Bureau of Shipping (ABS), Det Norske Veritas (DNV), Bureau Veritas (BV), and Rina. Hydroweld FS wet welding electrodes are currently the only wet underwater welding electrodes approved for permanent and temporary repairs on war ships by the British Ministry of Defense (MoD). This was gained after intensive underwater comparability testing and further NDE and destructive testing against all other commercially available wet welding electrodes by the MoD and The Welding Institute (TWI). As a result, the electrodes are now included in the NATO codification system.
To learn more about underwater welding at Subsea Global Solutions, review our latest underwater welding case study.